What Makes the Cost To Stain a Deck Go Up?
July 10th, 2024
4 min read
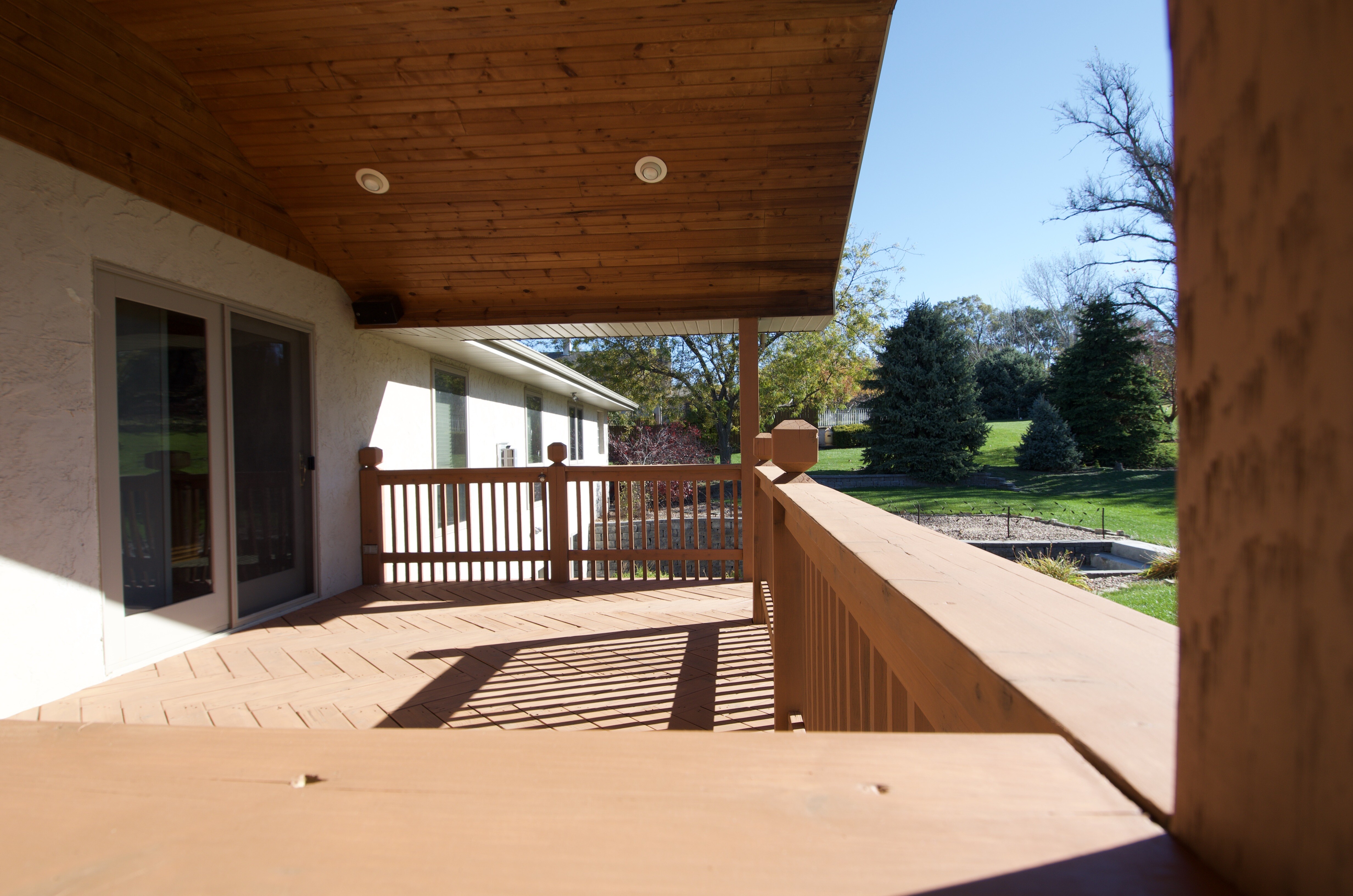
Deck staining is a crucial job for keeping up with the maintenance of your deck. However, we know times are tough and it can be hard to invest in your deck at the moment. You’re likely looking for a lower cost for your project, but don’t want to sacrifice quality.
One thing that can help you during this time, is to know a ballpark price of your project and what influences the cost, before getting quotes for the project.
At Brush & Roll Painting, we understand the factors that can drive up the cost of deck staining. With years of experience, since 1996, serving homeowners in Omaha, we’ve seen and handled it all, ensuring high-quality results every time.
In this article, we'll explain the reasons behind what makes a quote for deck, pergola, or fence staining project increase. By reading this article, you will know an average cost for your project,
Factors Increasing the Cost of Deck Staining
1. Deck Size
The size of your deck is one of the most significant factors affecting the cost of staining. Larger decks require more stain, which increases the cost of materials. Additionally, a larger area takes more time to stain, which increases labor costs.
The time and effort required to evenly apply the stain over a vast surface area is the main factor for the price.
2. Type of Wood on Your Deck
Different types of wood used for decking can impact the cost of staining. Hardwoods, such as mahogany, ipe, or teak, are denser and more challenging to work with compared to softwoods like pine or cedar.
Hardwoods often require special types of stains that can penetrate their dense fibers. These stains are usually more expensive than those used for softwoods. Moreover, hardwoods may need more coats of stain to achieve the desired finish and protection, increasing both material and labor costs.
Softwoods, on the other hand, are generally easier to stain but may still require a thorough preparation process to ensure an even application. The wood type also affects how the stain absorbs and adheres.
Some woods may absorb the stain unevenly, necessitating additional coats or specific application techniques to achieve a consistent look. This not only increases the amount of stain needed but also extends the time required for the project, thus increasing labor costs.
3. Deck Repairs
Deck repairs are a crucial part of the staining process and can significantly affect the overall cost. Before staining, it is essential to ensure that the deck is in good structural condition. This includes fixing any cracks, splinters, or loose boards. Ignoring these repairs can lead to further damage and a shorter lifespan for the stain.
Cracks and Splinters: Cracks and splinters need to be sanded down or filled with wood filler to create a smooth surface for staining. This can be time-consuming and may require specialized tools and materials.
Loose Boards: Loose or warped boards need to be secured or replaced. This process can involve removing and replacing nails or screws and ensuring that the boards are level and secure.
Structural Damage: In some cases, there may be more significant structural damage that requires extensive repairs. This can include replacing large sections of the deck or reinforcing the support structure. These types of repairs are more labor-intensive and costly but are essential for the safety and longevity of the deck.
In severe cases, you may consider rebuilding your wooden deck or building a composite deck.
Each of these repair tasks adds to the overall labor and material costs. However, investing in these repairs before staining ensures a more durable and long-lasting finish, ultimately saving money on future maintenance and repairs.
4. Quality of Deck Stain Product
The quality of the stain used on your deck can have a significant impact on the cost and longevity of the project. Higher-quality stains, while more expensive initially, offer better protection and durability. They are formulated to withstand harsh weather conditions, UV rays, and foot traffic, ensuring that the deck maintains its appearance and structural integrity for a longer period.
Durability: Premium stains are designed to penetrate the wood deeply, providing a longer-lasting finish. This means that the deck will require less frequent re-staining, saving money on maintenance over time.
Protection: High-quality stains offer superior protection against moisture, preventing issues like mold, mildew, and rot. This is especially important in Omaha, where weather conditions can vary widely, and the deck is exposed to both intense sun and heavy rain.
Aesthetic Appeal: Better quality stains provide a richer, more uniform color, enhancing the natural beauty of the wood. They also tend to fade less over time, keeping the deck looking fresh and vibrant for longer.
While the initial cost of high-quality stains is higher, the long-term benefits often outweigh the additional expense. Investing in a premium stain can extend the lifespan of your deck, reduce maintenance needs, and provide a better overall appearance.
5. Complexity of Your Deck Design
The design and layout of your deck, pergola, or fence can significantly influence the cost of staining.
Intricate Designs: Decks with detailed patterns or unique layouts require meticulous attention to ensure that every nook and cranny is adequately stained. This can involve using smaller brushes or special tools to reach tight spaces, adding to the labor time.
Multiple Levels: Multi-level decks are more challenging to stain because each level needs to be treated separately. Moving between levels, ensuring an even application, and managing the drying process can all add to the time and complexity of the project.
Railings and Stairs: Staining wooden railings and stairs is a detailed task that requires precision. These areas often need additional prep work, such as sanding and cleaning, to ensure the stain adheres properly. The vertical surfaces of railings and the horizontal steps of stairs need careful attention to avoid drips and ensure a uniform finish.
Built-In Features: Features like built-in seating, planters, or pergolas add to the staining workload. These elements often require extra preparation and careful staining to match the rest of the deck.
The more complex the deck design, the more labor-intensive the staining process becomes. This increases the overall cost but ensures a thorough and professional finish that enhances the deck's appearance and durability.
Average Cost of Deck Staining in Omaha
Cost of Staining Small Decks
- Average size: 10x12
- Cost range: $1,600 - $2400
Cost of Staining Medium-sized Decks
- Average size: 15x18
- Cost range: $2,400 - $3,600
Cost of Staining Large Decks
- Average size: 20x25 +
- Cost range: $3,600+
The Cost of Staining Your Deck
Maintaining your deck with regular staining can extend its life and keep it looking great. While several factors can increase the cost, understanding these can help you plan better for the project and avoid surprises.
Brush & Roll Painting is here to guide you through every step, ensuring your deck gets the care it deserves. With our expertise, you can confidently tackle your next deck staining project.
Another resource to help you stay confident throughout your deck-staining project is a checklist. This checklist allows you to cross off each decision and step of the project as it goes.
Kaylea is the Brush & Roll Painting Content Manager. Kaylea is a Journalism and Media Communications summa cum laude graduate with a minor in Marketing from the University of Nebraska at Omaha. Kaylea manages the marketing for Brush & Roll Painting.
Topics: